Bio-Inspired Micro- and Nanorobotics Driven by Magnetic Field
- PMID: 36363368
- PMCID: PMC9653604
- DOI: 10.3390/ma15217781
Bio-Inspired Micro- and Nanorobotics Driven by Magnetic Field
Abstract
In recent years, there has been explosive growth in the number of investigations devoted to the development and study of biomimetic micro- and nanorobots. The present review is dedicated to novel bioinspired magnetic micro- and nanodevices that can be remotely controlled by an external magnetic field. This approach to actuate micro- and nanorobots is non-invasive and absolutely harmless for living organisms in vivo and cell microsurgery, and is very promising for medicine in the near future. Particular attention has been paid to the latest advances in the rapidly developing field of designing polymer-based flexible and rigid magnetic composites and fabricating structures inspired by living micro-objects and organisms. The physical principles underlying the functioning of hybrid bio-inspired magnetic miniature robots, sensors, and actuators are considered in this review, and key practical applications and challenges are analyzed as well.
Keywords: bio-inspired robots; biomimetic materials; magnetic composite; magnetic field; magnetic micro-/nanorobots; soft robotics.
Conflict of interest statement
The authors declare no conflict of interest.
Figures
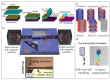
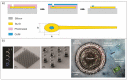
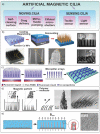
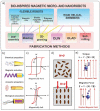
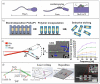
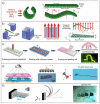
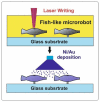
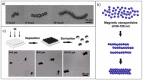
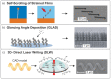
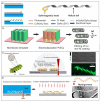
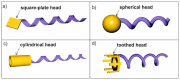
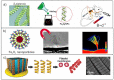
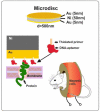
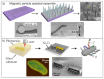
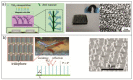
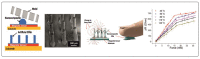
Similar articles
-
Special section on biomimetics of movement.Bioinspir Biomim. 2011 Dec;6(4):040201. doi: 10.1088/1748-3182/6/4/040201. Epub 2011 Nov 29. Bioinspir Biomim. 2011. PMID: 22128305
-
Programmable Morphing Hydrogels for Soft Actuators and Robots: From Structure Designs to Active Functions.Acc Chem Res. 2022 Jun 7;55(11):1533-1545. doi: 10.1021/acs.accounts.2c00046. Epub 2022 Apr 12. Acc Chem Res. 2022. PMID: 35413187
-
A Fully Three-Dimensional Printed Inchworm-Inspired Soft Robot with Magnetic Actuation.Soft Robot. 2019 Jun;6(3):333-345. doi: 10.1089/soro.2018.0082. Epub 2019 Feb 5. Soft Robot. 2019. PMID: 30720388
-
Design, fabrication and application of magnetically actuated micro/nanorobots: a review.Nanotechnology. 2022 Jan 18;33(15). doi: 10.1088/1361-6528/ac43e6. Nanotechnology. 2022. PMID: 34915458 Review.
-
Recent progress in magnetic applications for micro- and nanorobots.Beilstein J Nanotechnol. 2021 Jul 19;12:744-755. doi: 10.3762/bjnano.12.58. eCollection 2021. Beilstein J Nanotechnol. 2021. PMID: 34367858 Free PMC article. Review.
Cited by
-
Bio-Hybrid Magnetic Robots: From Bioengineering to Targeted Therapy.Bioengineering (Basel). 2024 Mar 26;11(4):311. doi: 10.3390/bioengineering11040311. Bioengineering (Basel). 2024. PMID: 38671732 Free PMC article. Review.
-
Advances in smart delivery of magnetic field-targeted drugs in cardiovascular diseases.Drug Deliv. 2023 Dec;30(1):2256495. doi: 10.1080/10717544.2023.2256495. Drug Deliv. 2023. PMID: 37702067 Free PMC article. Review.
-
A Nanorobotics-Based Approach of Breast Cancer in the Nanotechnology Era.Int J Mol Sci. 2024 May 2;25(9):4981. doi: 10.3390/ijms25094981. Int J Mol Sci. 2024. PMID: 38732200 Free PMC article. Review.
-
Magnetic Microrobots for In Vivo Cargo Delivery: A Review.Micromachines (Basel). 2024 May 20;15(5):664. doi: 10.3390/mi15050664. Micromachines (Basel). 2024. PMID: 38793237 Free PMC article. Review.
References
-
- Ummat A., Dubey A., Mavroidis C. Biomimetics: Biologically Inspired Technologies. CRC Press; Boca Raton, FL, USA: 2005.
-
- Stroble J.K., Stone R.B., Watkins S.E. An overview of biomimetic sensor technology. Sens. Rev. 2009;29:112. doi: 10.1108/02602280910936219. - DOI
-
- Lu L., Hu X., Zhu Z. Biomimetic sensors and biosensors for qualitative and quantitative analyses of five basic tastes. Trend. Anal. Chem. 2017;87:58. doi: 10.1016/j.trac.2016.12.007. - DOI
Publication types
LinkOut - more resources
Full Text Sources